- HOME
- プラスチック加工のワンポイント講座
- プラスチック加工とは?樹脂切削加工の基礎
プラスチック加工とは?樹脂切削加工の基礎
プラスチック加工の基本
プラスチック加工とは
プラスチック加工とは、様々な用途に対応できるプラスチック材質を、私たちの生活に役立つ製品へと変えるための加工技術です。丸材・板材からの削り出し、原料となる樹脂からの成形で、目的の形状や性質を持つ製品へと加工します。プラスチック加工は、製品の製造に欠かせない技術であり、その応用範囲は非常に広いです。
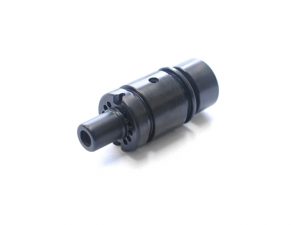
プラスチックの特性
プラスチックは、軽量で強度があり、加工性に優れた材質です。これらの特性を生かして、様々な製品が作られています。例えば、軽量で耐久性に優れたプラスチックは、自動車や航空機などの輸送機器の部品に多く用いられています。また、耐熱性や耐薬品性に優れたプラスチック材質は、電子機器や医療機器などの精密機器の部品に用いられています。
プラスチックの種類は多岐にわたります。プラスチック部品の製作は、それがどういった環境下で使用されるか、どんな機能性が要求されるか、ということを考えながら材質選定をする必要があります。
プラスチック加工の種類
プラスチック加工方法は主に切削加工・3Dプリンター出力・成形の3つです。
切削加工
マシニングや同時五軸、NC旋盤等の工作機械を用いる加工方法です。切削加工の特徴は、プラスチック材料のブロックやロッドを刃物で削り、形状を仕上げていく加工方法であるということです。基本的に各材料メーカーから販売されている規格品の材料から削り出していきます。
1個1個製作する加工方法のため、数千個レベルの量産には不向きです。1個~1000個程度の小ロットや、試作品の製作に適しています。
3Dプリンター出力
3Dプリント技術は、コンピュータで設計した3次元モデルに基づいて、プラスチックなどの材料を積層して立体物を作る技術です。3Dプリント技術は、従来の加工方法では実現できなかった複雑な形状の製品を製造することができるため、近年注目されています。3Dプリント技術は、試作品製作や少量生産に適しています。
成形加工
成形加工法は、プラスチックを熱や圧力を加えて、目的の形状に成形する加工方法です。成形加工法には、射出成形、押出成形、ブロー成形、真空成形などがあります。射出成形は、溶融したプラスチックを金型に注入して成形する方法で、大量生産に適しています。押出成形は、溶融したプラスチックを金型に通して連続的に成形する方法で、パイプやフィルムなどの製造に適しています。ブロー成形は、溶融したプラスチックを金型に吹き込んで成形する方法で、ボトルや容器などの製造に適しています。真空成形は、シート状のプラスチックを金型に吸着させて成形する方法で、複雑な形状の製品の製造に適しています。
樹脂切削加工で押さえておくべきポイント
プラスチック材質の特性
プラスチックは金属とは異なり、気温や湿度の影響を非常に受けやすい材質です。材料によっては朝・昼・晩の室温の変化の影響を受けて収縮・膨張することがあります。そのため、金属では対応可能な公差が樹脂では対応不可、という場合もあります。特に千分台の公差の管理をプラスチック材質で行うことは非常に難しいです。
また、長期保管にも注意が必要です。気温の他に湿度の影響も受けるため、乾燥している冬と湿度の高い夏を跨いで長期保管すると、製作時は嵌合していた部品が嵌合できなくなっている、という事例もあります。そのため、一定の気温・湿度を保てる空間で保管することが推奨されます。
切削加工の特徴
切削加工は材料費+加工費で製品の価格が算出されます。材料費よりも加工費の方が単価に影響を与えることが多いため、設計段階でのコストダウン意識が大きな意味を持ちます。
刃物R
切削加工は工作機械を使用し、刃物で材料を削り製品を仕上げていく加工方法です。マシニング加工の場合、円形の刃物が回転しながら材料を削ります。例えば板の中心に正方形の穴を開けます。
円形の刃物は回転しながら進むため、四隅を直角に仕上げることができず、必ずRがつきます。(直角の四隅に限らず、鋭角に仕上げることができないのが特徴です)。Rの大きさは刃物径に依存するので、Rを小さくしてできる限り直角に近付けようとすると細い刃物で加工する必要があります。
しかし、細い刃物はどうしても強度が弱くなってしまうため、硬い材質の場合刃物が折れてしまい、時間がかかりコストに影響を与えます。そのため、コストを抑えて製作を検討する際はこのようなRを考慮した上で設計するか、逃がし穴を作り直角を作りだすことを推奨します。
旋盤加工では、材料が回転し刃物が固定されているので、Rが付かないようにも考えられますが、刃物の先端が鋭角ではなく小さいRがついています(一般的な工具でR0.4程度)。そのため、旋盤での加工品もマシニング加工と同様に角部は直角にはならずRがついている形状になります。
刃物の径と深さ
刃物は径が細くなるにつれて折れやすくなります。その径が細い刃物で深い穴や、刃物が届きにくい箇所を加工する場合、さらに長い刃物を使用します。径が細く、長さが長いものは先端(刃物部分)がブレやすいため、切削条件(速度等)を調整して慎重に加工します。
お問い合わせ
プラスチック切削加工のご相談は
「即レスポンス・短納期の湯本電機」へ!